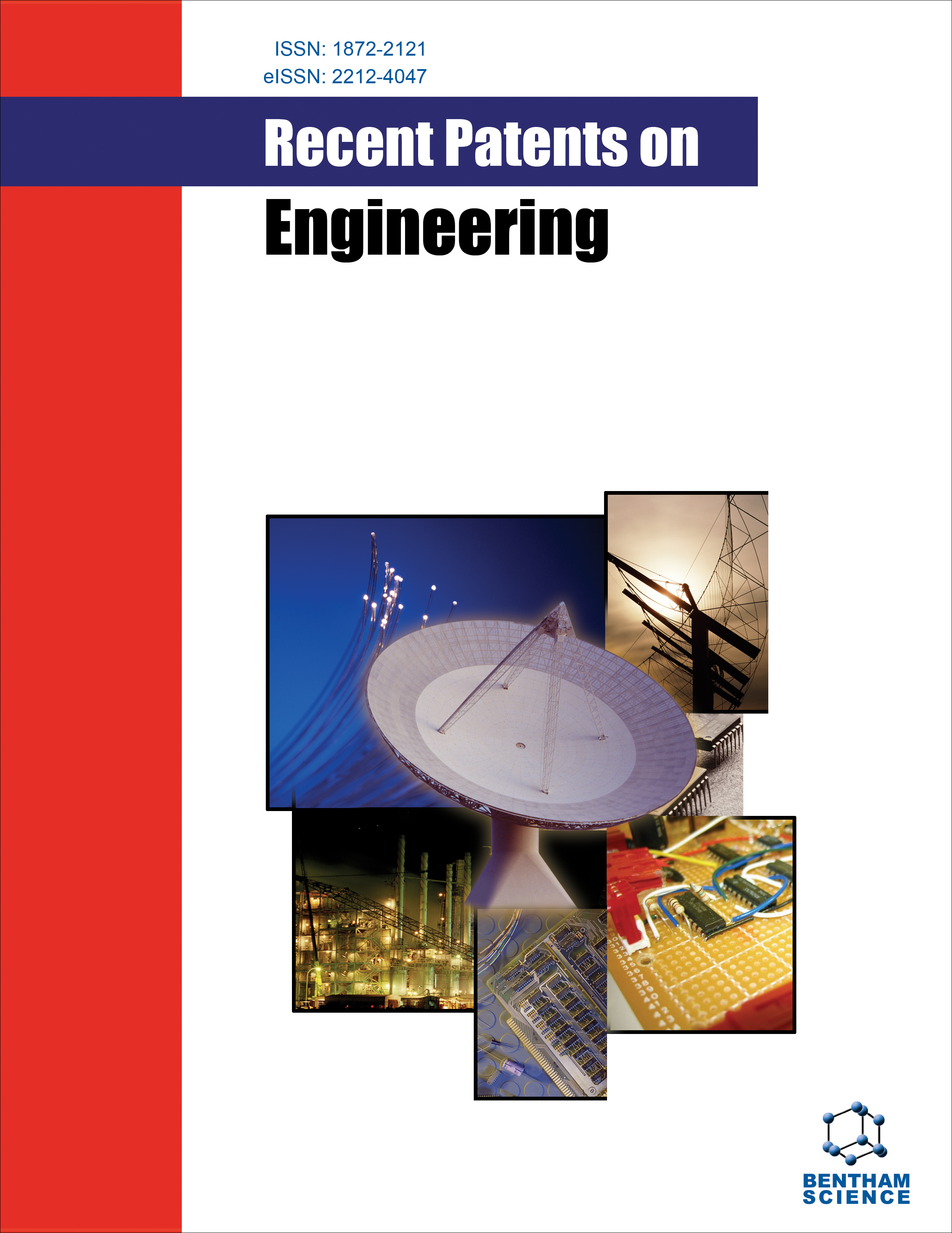
-
oa Advances in the Experimental Research on the Surface Integrity in the Cutting of Titanium Alloy
-
-
- 11 Aug 2024
- 24 Sep 2024
- 09 Dec 2024
Abstract
Titanium alloy, as a high-strength alloy material, has been widely used in aerospace and other fields due to its high specific strength, good corrosion resistance, super fracture toughness, and fatigue resistance. However, its small elastic modulus, low thermal conductivity, and strong chemical affinity result in high cutting forces and cutting temperatures during the cutting process. Different thermo-mechanical coupling effects can change the surface structure, composition, and mechanical properties of the workpiece and show different surface integrity. This paper summarizes the recent progress in the experimental research on surface integrity in the cutting of titanium alloy from four aspects, including surface roughness, microhardness, white layer, and residual stress. It focuses on analyzing the experimental results about the influence of process parameters, tool wear, and lubrication methods on surface integrity. The problems existing in current research and the future development direction are pointed out in this article. It is helpful to provide theoretical guidance for the machining of titanium alloy that meets the requirement of service performance.
Surface integrity encompasses both geometric features and physical and mechanical properties. Geometric features include surface roughness, surface morphology, and blade direction. Extensive research has been conducted on surface roughness, microhardness, the white layer, and residual stress. This article reviews recent advancements in experimental research on surface integrity during titanium alloy cutting, focusing on the impact of cutting parameters, tool wear, and lubrication methods. It also addresses current research challenges and suggests directions for future development.
Scholars have conducted extensive research on surface roughness, microhardness, the white layer, and residual stress using both experimental methods and finite element simulations. Experiments are the primary method due to existing issues with finite element simulations, which often suffer from low accuracy and poor reliability in studying surface integrity during titanium alloy machining.
At present, a large amount of experiments have been conducted. However, due to the numerous influencing factors and insufficient consideration of materials microstructure, the conclusions of current research are not consistent. Therefore, it is necessary to conduct more in-depth and systematic experimental research to clarify the influencing factors and the influence of cutting parameters on surface integrity.
There is a need for a deeper understanding of the physical and mechanical fundamentals of surface integrity. Integrating experimental research with finite element simulations can enhance the investigation of these mechanisms and improve predictions related to phase transformation, microhardness, white layer, and residual stress. It is helpful to provide theoretical guidance for the machining of titanium alloy that meets the requirement of service performance.