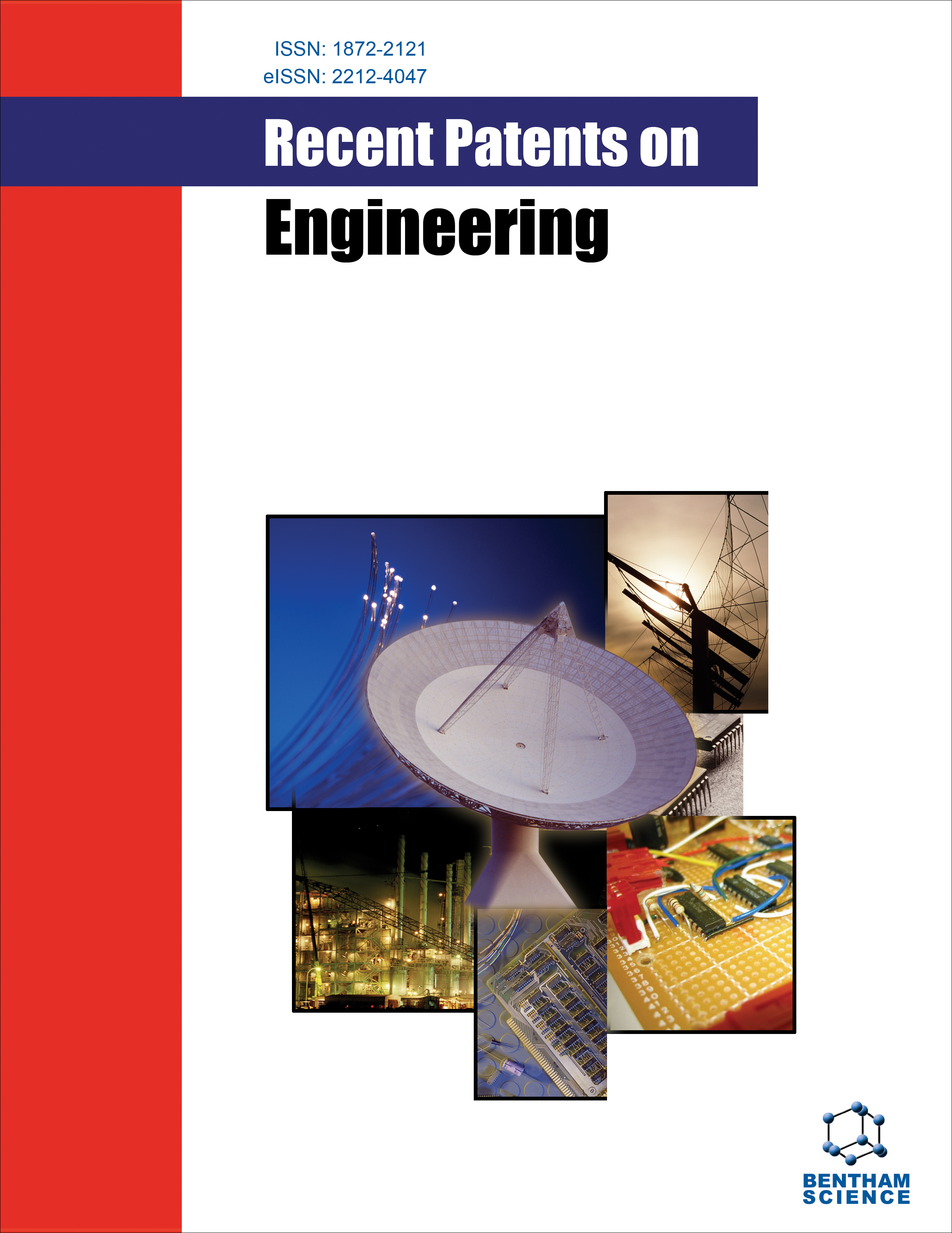
-
oa Experimental Study on the Influence of Stand-Off of Directional Measurement While Drilling (MWD) Instrument With Barrel
-
-
- 16 Sep 2024
- 21 Oct 2024
- 10 Dec 2024
Abstract
Firstly, the mapping relationship between the make-up torque and the axial preload of directional Measurement While Drilling (MWD) instruments was obtained. Next, the influence of thread joint stand-off deviation on their conversion relationship was studied. Finally, the make-up work of the instrument was guided effectively.
This patent research aims to investigate the make-up process of the MWD instruments and the impact of stand-off.
The experiment was designed to map the relationship between the make-up torque and axial pre-tightening force of the directional MWD instrument with a barrel. The influence of the thread joint stand-off deviation on the said relationship was studied.
Test results have shown that the relationship between the make-up torque and the axial preloading force is nonlinear. Further, in the American Petroleum Institute (API) standard, the relationship between the two is defined as linear, increasing the effect of preloading within the high torque range.
For identical make-up torques, the threaded joint with positive stand-off produced a smaller axial preloading force compared to its counterpart with negative stand-off. However, a large enough make-up torque reduced the influence of the threaded joint stand-off deviation on the make-up torque-axial preloading force.