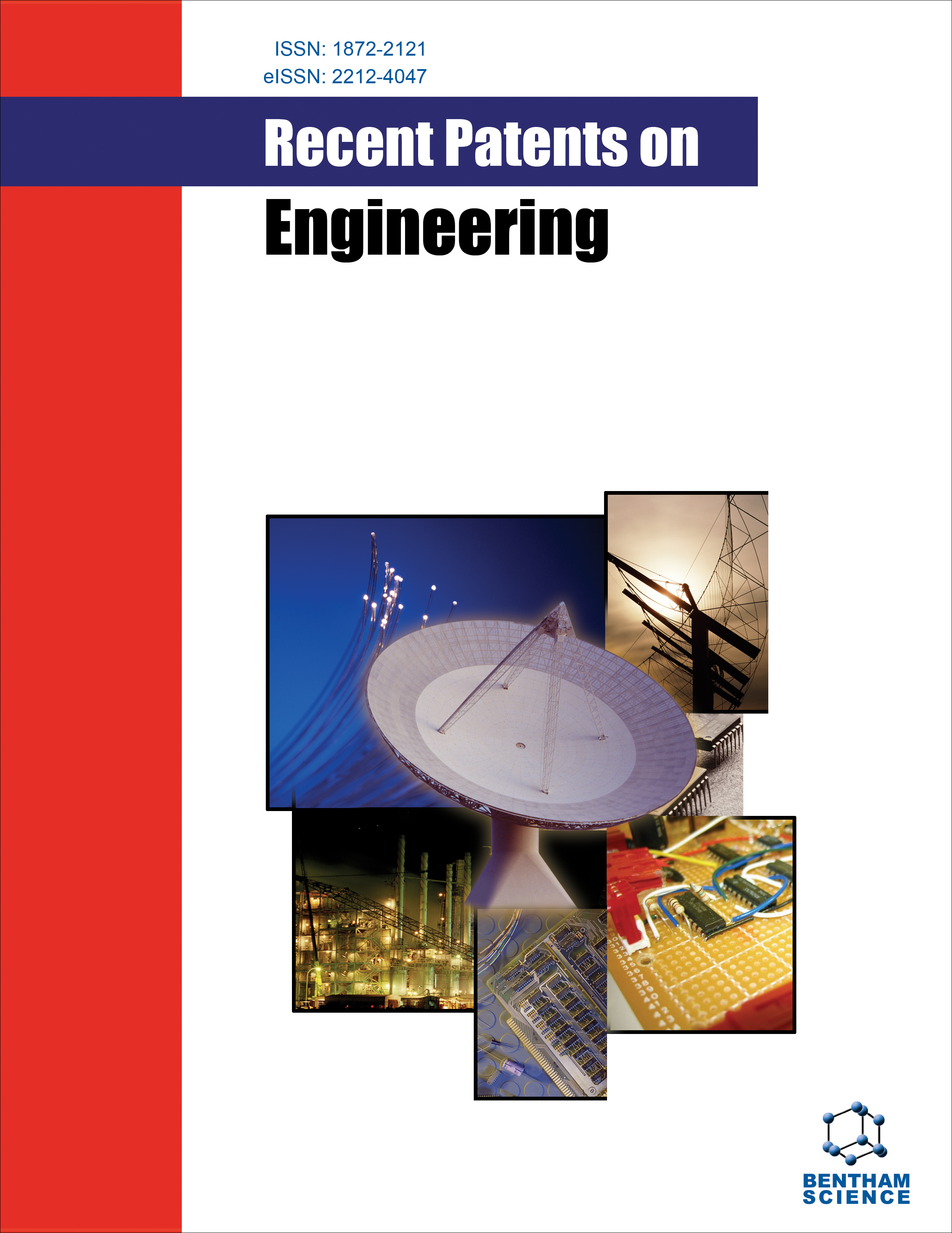
-
oa Recent Patents on Cageless Rolling Bearings
-
-
- 09 May 2024
- 05 Aug 2024
- 04 Dec 2024
Abstract
Rolling bearings are widely used as core components in mechanical equipment. Most bearings are equipped with a cage. However, when bearings work under conditions of large load and high speed, the cage will produce violent friction and collision between the rolling body and the rings of the bearing, which will reduce the stability of the bearing operation and even fracture the cage. Bearing cage significantly impacts the rotational accuracy and life of the bearing. Therefore, in recent years, many scholars have begun researching cageless rolling bearings. The cageless rolling bearing eliminates the various adverse effects brought about by the cage and reduces the weight of the bearing. However, the bearing structure must be reasonably designed to eliminate the reverse friction between adjacent rolling elements in cageless cases. Therefore, it is essential to design the structure of cageless rolling bearings and study their performance.
By analyzing and summarizing the research on cageless rolling bearings in recent years, the current problems and the future development of cageless rolling bearings are analyzed to provide a reference for researchers in the related fields.
This paper reviews representative patents related to cageless rolling bearings, discusses the structure and performance of various cageless rolling bearings, and analyzes their advantages and disadvantages, mainly including full complement cageless bearings, isolation element bearings, and special cageless bearings. Each type of bearing is analyzed through ball bearings and roller bearings.
Through the analysis of the related patents on cageless rolling bearings, it is found that the main problems affecting the development of cageless rolling bearings are the irregular collision of rolling elements with each other, the friction between rolling elements and the adjacent elements, and the difficulty in machining the particular shape isolation and raceway. Future research focuses on how to improve the service performance of cageless rolling bearings comprehensively so that they can work under high speed and heavy load.
Cageless rolling bearings simplify the bearing structure to increase the number of rolling elements. Therefore, the capacity of the rolling bearing is improved. The internal bearing friction can be reduced through structural innovation design. Cageless rolling bearings have broad development prospects